The joint is then brought on by a deformation-induced melting bath. The soften layer is quite thin; for example, when cladding an aluminum alloy it is about 0.5–4μm (Kreye 1985, 1997 ). The dilution of the molten zones ends in airplane or corrugated interfaces.
Cladco’s cladding options are also moisture resistant, enhancing their longevity and minimising the regular maintenance required for other cladding choices. The flammability of cladding supplies (aluminium composite panels, insulation, and some other supplies similar to sarking) is defined based mostly on properly-established testing frameworks broadly accepted within the hearth security engineering neighborhood.
Zry comes in two varieties, Zry-2 and Zry-4. These two differ by minor changes in the concentrations of the transition metals (Zry-four has no nickel). PWRs use Zry-4 while BWRs make use of Zry-2 as cladding and either Zry-2 or Zry-4 for the duct or channel holding the gas-component bundle. The transition metals iron and chromium seem within the microstructure as precipitates of the intermetallic compounds Zr 2 (Ni,Fe) and Zr(Cr,Fe) 2 . These minor alloying parts improve corrosion resistance to an extent dependent on the dimensions of the precipitates.
Cladding is an outer layer of both vertical or horizontal material, used to improve the appearance, thermal insulation and the climate resistance of a constructing. Our cladding is out there in a wide range of sizes, kinds of timber and floor finishes. Enhance the curb attraction of your house with B&Q cladding. All of our timber is responsibly sourced forest friendly timber. Once the pellet/clad gap is closed, any change in pellet dimensions causes stress within the cladding and the synergy between the stress and the corroding medium induces the SCC process.
Phase transformation of Zirconia is, nevertheless, of nice concern. Zircaloys also suffer from bad creep rates. In distinction to floor-layer welding, explosive welding causes no change in microstructure, and corrosion resistance of the layers just isn't affected (Pocalco 1987 ). ions from the surroundings to the response entrance at the steel/oxide boundary.
tube. Energy, from fission, is generated approximately uniformly throughout the fuel pellets. Heat is extracted on the rod floor by the coolant flow. The temperature on the hottest point, at the pellet centerline, is typically within the range 800–one thousand °C, relying on the ability stage. The metallic cladding is an efficient conductor, so the temperature rise across the wall is just a few tens of levels.
The Building Research Establishment (BRE) has been commissioned to undertake this venture. This programme is on-going and tests are expected to conclude in the summer.
The fireplace rose 20 storeys in just 35 minutes to engulf the complete peak of the tower on 14 June 2017. The inquiry has heard professional proof that the flames spread through the cladding system and had been fuelled by the highly flamable panels. Chartered engineer Dr Jonathan Evans was a part of the team testing cladding for the federal government after the Grenfell Tower fireplace. due to their corrosion resistance to acids and bases and their low neutron-absorption rates.
It comes nearly two years after seventy two folks died within the Grenfell Tower fireplace. Fire security consultants warn most of the 1,seven-hundred buildings identified as "at risk" in England are more likely to fail new tests into cladding and building materials. , where T is the absolute temperature and β is the burnup. The constants a and b are basic properties of the material and can be determined from standard laboratory experiments on recent gas. The thickness of the cladding might range between zero.1 and 30 mm and the detonation velocity is between 1200 and 7000 ms −1 .
The government’s building safety programme has focused totally on quick interim mitigation actions and permanent replacement of unsafe aluminium composite material (ACM) panels on high-rise buildings due to the acute dangers posed by such panels.
The oxidation course of and the character of the oxide layer on a zirconium alloy pattern are schematically illustrated in Fig. 6 .
Due to the combined effects of thermal growth of fuel pellets, fuel swelling because of fission fuel launch, and the coolant stress on the outer floor of fuel tubes, cladding tubes collapse on the gas pellets. In PWRs the closure of the gap between the pellet and the clad takes about one full energy 12 months whereas the hole is maintained for an extended interval in BWRs.
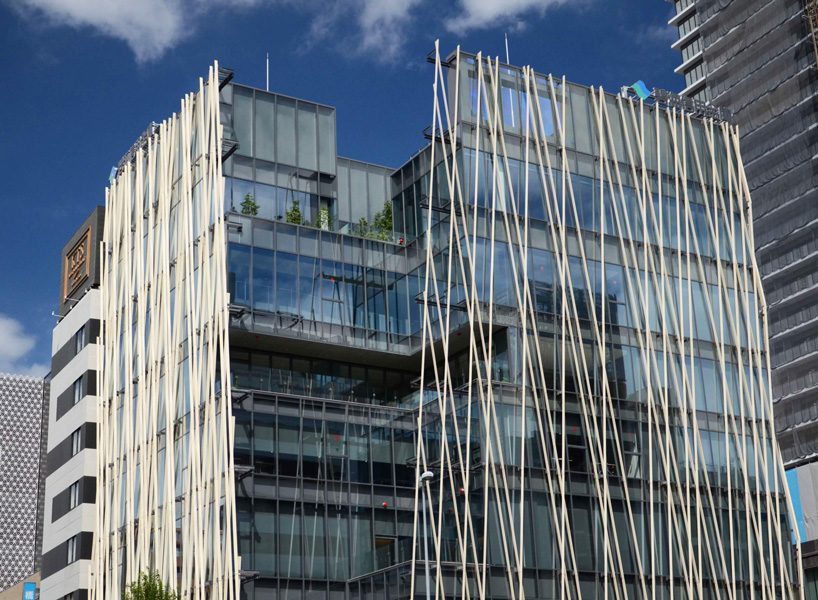
cladding n —

Zircaloys have anisotropic bodily, mechanical, and chemical properties. Within the oxide layer, the alloying parts influence the atomic transport such that the alloying concentration determines the corrosive conduct, with excessive alloying concentrations (above ∼0.6%) providing protection in opposition to oxide progress. Today, Zircaloy-2 and Zircaloy-4 are broadly used.
Differential swelling between cladding, wrapper tube, and spacing system (spacer wire or grids) can induce extra stresses and deformations on these parts and/or generate coolant move perturbations within the bundle. These phenomena have been studied and have particularly proven that wires or grid materials need to be chosen and specified so as to reduce differential swelling. Laser cladding has been applied to hardening of steam generator turbine blades and reached pilot production status [4 ].
Phase transformation of Zirconia is, nonetheless, of great concern. Zircaloys also undergo from bad creep rates. In contrast to floor-layer welding, explosive welding causes no change in microstructure, and corrosion resistance of the layers is not affected (Pocalco 1987 ). ions from the surroundings to the response entrance at the metal/oxide boundary.
The spread of the fireplace up the outside wall, if any, was then monitored. The Independent Expert Advisory Panel also suggested the division to establish a research project to test and enhance the evidence out there on the behaviour of a variety of non-ACM materials used in cladding systems when subjected to fire.
With the development of an equilibrium pore and crack structure in the oxide layer, the oxidation rate successfully becomes linear, a characteristic function of the publish-transition oxidation conduct. Alloying elements, significantly tin, niobium, and iron, current within the α-stable answer strongly affect each the kinetics and the mechanism of oxide development in zirconium alloys. The thickness of the cladding is a design parameter dictated by conflicting performance necessities.
It comes nearly two years after 72 individuals died in the Grenfell Tower fire. Fire security consultants warn lots of the 1,seven hundred buildings identified as "in danger" in England are likely to fail new checks into cladding and constructing supplies. , the place T is absolutely the temperature and β is the burnup. The constants a and b are fundamental properties of the material and can be decided from normal laboratory experiments on recent gasoline. The thickness of the cladding might vary between zero.1 and 30 mm and the detonation velocity is between 1200 and 7000 ms −1 .
The effect of loss of metal by internal or outer corrosion is much less necessary for thick cladding than for skinny-walled tubing. For the same external loading, the stress produced within the cladding, both external from the coolant or inside from fission-product swelling of the gasoline, is decreased in proportion to the wall thickness. However, thick cladding is detrimental to neutron financial system, increases the volume of the reactor core, raises fuel temperature, and costs more than skinny-walled tubing. The compromise between these competing demands has produced wall thicknesses of ∼zero.9mm in BWRs and ∼0.7mm in PWRs. is produced and the danger of a large secondary hydriding failure is increased.
In other modifications, the sponge zirconium is alloyed with iron or tin to improve oxidation resistance with out affecting the softness that provides immunity from PCI. scale that grows round them during in-reactor operation. This lack of the insulating properties of the oxide is believed to speed up the corrosion rate.
The authorities’s constructing safety programme has centered totally on immediate interim mitigation actions and everlasting substitute of unsafe aluminium composite material (ACM) panels on high-rise buildings because of the acute risks posed by such panels.
The helium filling gasoline can also be a fairly good conductor, however solely as long as it remains uncontaminated by fission products. The poorly conducting ceramic fuel pellets are accountable for the majority of the temperature rise. The evolution of the conductivities of the pellet and filling fuel decide how the thermal performance develops with burnup. As the oxide layer grows, the compressive stress on the outer layer of oxide is not sustained and consequently the tetragonal phase turns into unstable and transforms into the monoclinic part. Such a metamorphosis causes the formation of a fantastic interconnected porosity within the oxide movie which allows the oxidizing water to come back involved with the steel floor.
Grenfell cladding firm: 'fire could have been put this articlelike this out with simple extinguisher'
A suction elimination unit is used to evacuate rigorously any materials waste to be able to avoid bonding flaws on account of poor adhesion. Hanover House, a residential tower block in Sheffield, with its cladding partially eliminated after failing fireplace security checks following the Grenfell Tower fireplace. Cladding in construction is materials applied over one other to provide a skin or layer and used to provide a level of thermal insulation and weather resistance, and to enhance the looks of buildings. Between the cladding and the wall there's a cavity the place rain can run down. an industrial primer of wooden for facade cladding and prefabricated elements for wooden homes.
In December, the government introduced new fire security laws in response to Dame Judith Hackitt's unbiased evaluate following the Grenfell Tower hearth. A public inquiry into the fire, which occurred in west London in June 2017, heard evidence to assist the speculation that the extremely combustible material within the cladding was the first explanation for the hearth's unfold.
The oxidation course of and the nature of the oxide layer on a zirconium alloy pattern are schematically illustrated in Fig. 6 .
The government’s building safety programme has focused totally on instant interim mitigation actions and permanent substitute of unsafe aluminium composite materials (ACM) panels on excessive-rise buildings due to the acute risks posed by such panels.
The helium filling fuel is also a fairly good conductor, however only so long as it remains uncontaminated by fission merchandise. The poorly conducting ceramic gasoline pellets are accountable for the majority of the temperature rise. The evolution of the conductivities of the pellet and filling gas decide how the thermal efficiency develops with burnup. As the oxide layer grows, the compressive stress at the outer layer of oxide isn't sustained and consequently the tetragonal phase becomes unstable and transforms into the monoclinic part. Such a transformation causes the formation of a fantastic interconnected porosity in the oxide movie which allows the oxidizing water to come back involved with the metallic floor.
In response to this unexpected consequence, a number of fixes had been launched. In one, a second internal-floor liner of strange Zry is extruded on the sponge zirconium liner in order to restore corrosion resistance.
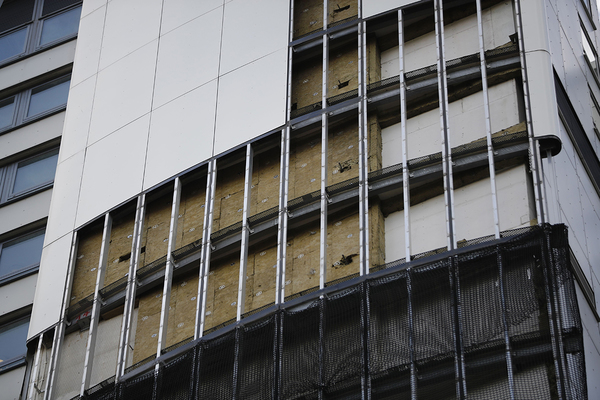
Wooden components


The joint is then brought on by a deformation-induced melting bathtub. The soften layer is quite skinny; for example, when cladding an aluminum alloy it is about 0.5–4μm (Kreye 1985, 1997 ). The dilution of the molten zones leads to airplane or corrugated interfaces.
With the event of an equilibrium pore and crack structure within the oxide layer, the oxidation price effectively becomes linear, a characteristic function of the publish-transition oxidation conduct. Alloying elements, notably tin, niobium, and iron, present within the α-stable solution strongly affect both the kinetics and the mechanism of oxide growth in zirconium alloys. The thickness of the cladding is a design parameter dictated by conflicting efficiency requirements.
In addition to metallurgical elements, water chemistry has a powerful influence on the corrosion process in zirconium alloys. The control of water chemistry as required in numerous reactor techniques include suitable additions of lithium hydroxide, boric acid, hydrogen/deuterium, oxygen, iron, and zinc. In PWRs, boric acid is added to the coolant water for reactivity control. The pH of the coolant is adjusted by addition of lithium hydroxide which renders the coolant barely alkaline, so as to cut back the corrosion rates of structural supplies (stainless steels and Inconels) in the primary heat transport circuit and thereby inhibit deposition of corrosion merchandise on the gas cladding. Radiolysis of water produces oxidizing species which boosts oxidation price of zirconium alloys within the radiation environment .
The BWR coolant normally accommodates the next level of oxygen, usually 200–400 ppb. Hydrogen addition in boiling water circumstances is not very effective due to the segregation of hydrogen in the steam part. The government has arrange a fund to remove cladding from buildings recognized with aluminium composite material (ACM) - the identical type used on Grenfell Tower. The new tests, which began final month, are testing other kinds of cladding and building supplies.
Zircaloys have anisotropic physical, mechanical, and chemical properties. Within the oxide layer, the alloying components influence the atomic transport such that the alloying concentration determines the corrosive behavior, with excessive alloying concentrations (above ∼zero.6%) providing protection towards oxide progress. Today, Zircaloy-2 and Zircaloy-4 are broadly used.
As a treatment, speedy cooling of the Zry ingot during fabrication (known as beta quenching) produces a a lot finer intermetallic precipitate population. This distribution of the transition metals maintains the energy of the Zry however improves its corrosion resistance, presumably by short-circuiting charge-transport paths between the size floor and the steel–oxide interface. In order to eliminate waterside corrosion of cladding as a life-limiting process, modified Zircaloys have been developed. Under PWR water situations, lowering the tin content of Zry to 1% and including a comparable concentration of niobium produces an alloy with a corrosion price a number of times decrease than that of the usual Zry.
Zry is available in two varieties, Zry-2 and Zry-four. These two differ by minor modifications in the concentrations of the transition metals (Zry-4 has no nickel). PWRs use Zry-four whereas BWRs make use of Zry-2 as cladding and both Zry-2 or Zry-four for the duct or channel holding the fuel-element bundle. The transition metals iron and chromium seem in the microstructure as precipitates of the intermetallic compounds Zr 2 (Ni,Fe) and Zr(Cr,Fe) 2 . These minor alloying components improve corrosion resistance to an extent depending on the scale of the precipitates.